Enhancing Safety and Precision in the Lab with EXAKT Pathology Saws
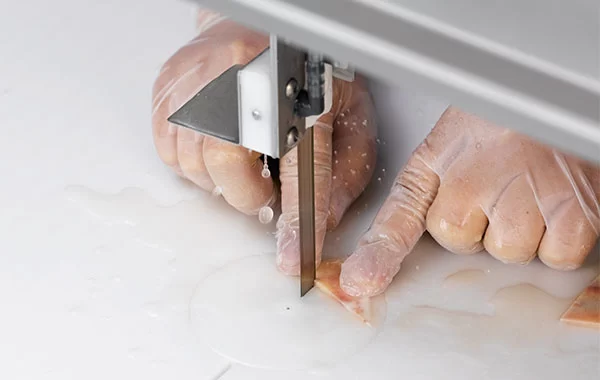
In the demanding environment of pathology labs, precision and safety are paramount. EXAKT Pathology Saws have emerged as an essential tool for medical professionals, combining innovative features that ensure accurate cuts and minimize the risk of injuries. Here’s how these advanced saws contribute to a safer and more efficient workspace. Precision and Effortless Cutting One […]
Precision and Safety in Grossing
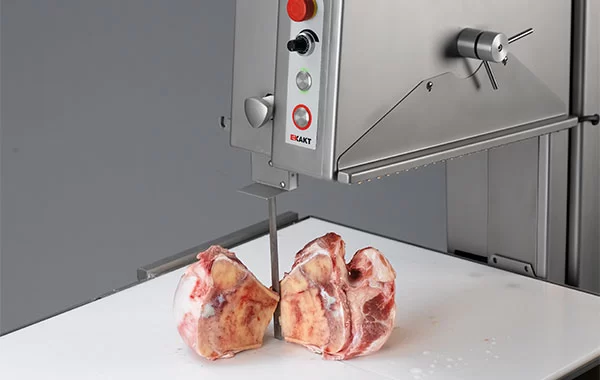
EXAKT’s 312 Pathology Saw: Precision and Safety in Grossing When it comes to pathology, the EXAKT 312 Pathology Saw is a game-changer, offering exceptional performance for grossing tissue and bone samples. Here’s why: Unmatched Safety The EXAKT 312 is designed with safety in mind. Its exclusive diamond band grinds rather than cuts, virtually eliminating the […]
How EXAKT Three Roll Mills Create Better Ceramic Products
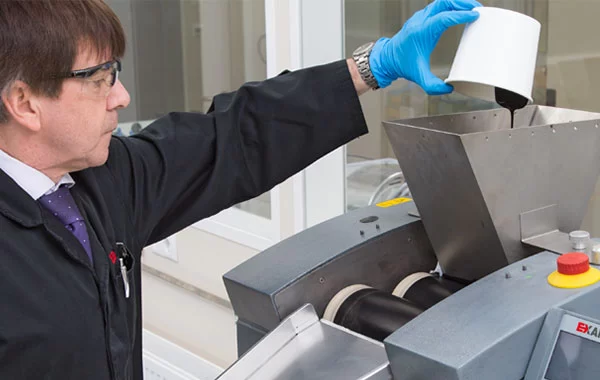
EXAKT three-roll mills contribute to the creation of better ceramic products through several key mechanisms: Uniform Dispersion: By effectively breaking down agglomerates and distributing ceramic powders and additives uniformly throughout the matrix, EXAKT three-roll mills ensure homogeneity in ceramic formulations. This leads to consistent material properties, such as mechanical strength, thermal stability, and chemical resistance, […]
6 Highlights of the EXAKT 80S Plus
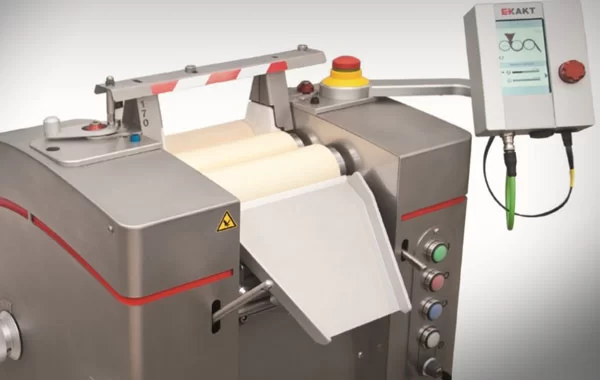
Improved safety standards, easy operation, and even more precise adjustment of the gap. The EXAKT 80S PLUS has higher safety standards, easier operation, and an even more precise adjustment of the gap. With a powerful motor, optional temperature control, and the choice of ceramic and metallic rollers, the 80S Plus was designed for processing a […]
EXAKT Pathology Saws Operate with Speed
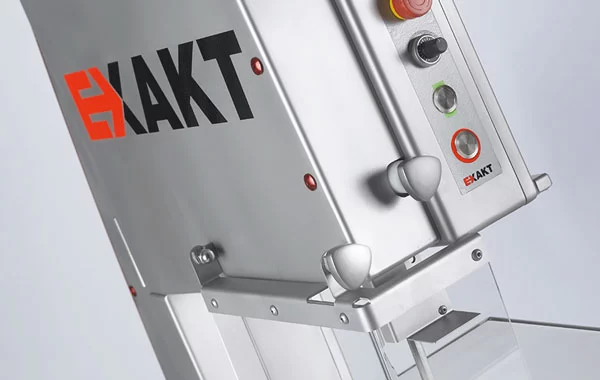
Process specimens quickly and accurately with the EXAKT Pathology Saws. Because the saws were developed in cooperation with hospitals and universities, the 312 and 302 fit perfectly in fast routine operations. Obtain pristine results on the very first cut Quick and easy setup and clean up with built-in water jet Access and change the diamond […]
5 Reasons EXAKT Ointment Mills Are Better Than Mixers
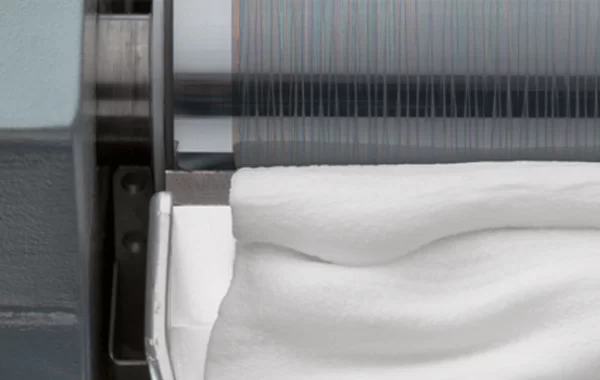
A comparative study conducted at the University of Hamburg, Institute of Pharmacy in Hamburg Germany concluded that the quality of compounds processed with EXAKT ointment mills is better than those processed with electric mixing systems. The particle size is smaller and the particle size distribution is more narrow. Ointment stability is better. Temperatures do not […]
EXAKT Pathology Saws Make Cleanup Easy
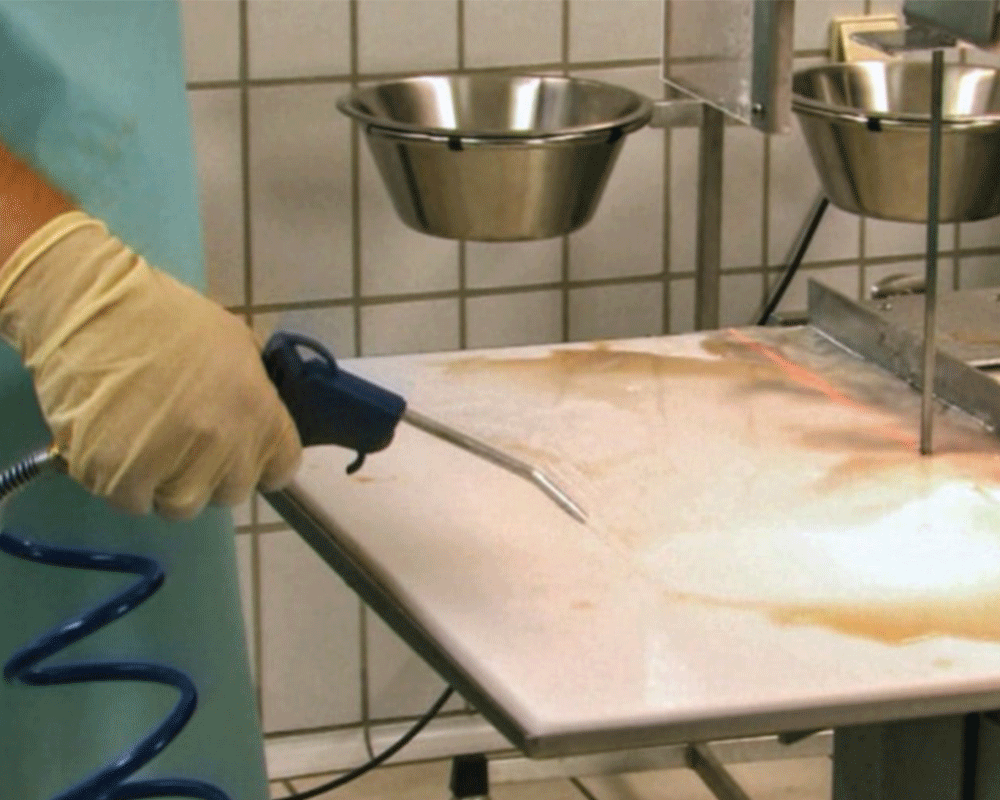
The EXAKT pathology saws make cleanup easy. Really easy! You can see how easy here. The stainless steel housing is designed for the optimum discharge of water and tissue; easy to disinfect. All run-off surfaces are sloped. No tools are needed. Key elements of the saw-like the doors, the top of the work table, or […]
EXAKT Pathology Saws are extremely easy to operate
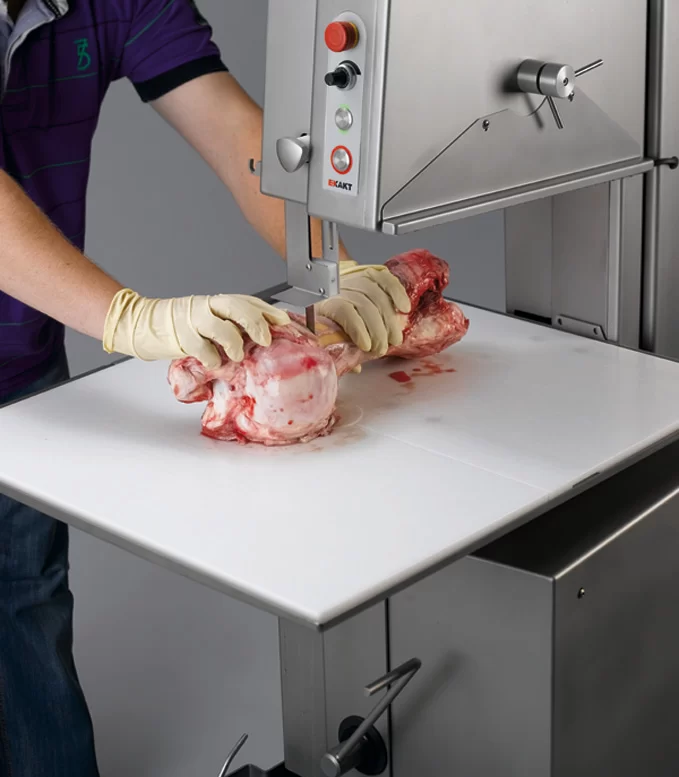
EXAKT Pathology Saws are extremely easy to operate. The housing simply opens and closes with magnetic catches; the band can be replaced without tools. Large pulleys contribute to the long service life of the diamond band. Grosses very small, very large, and loose specimens with ease and precision. A built-in laser guide makes the cutting […]
When to replace the guides and scraper on your ointment mill
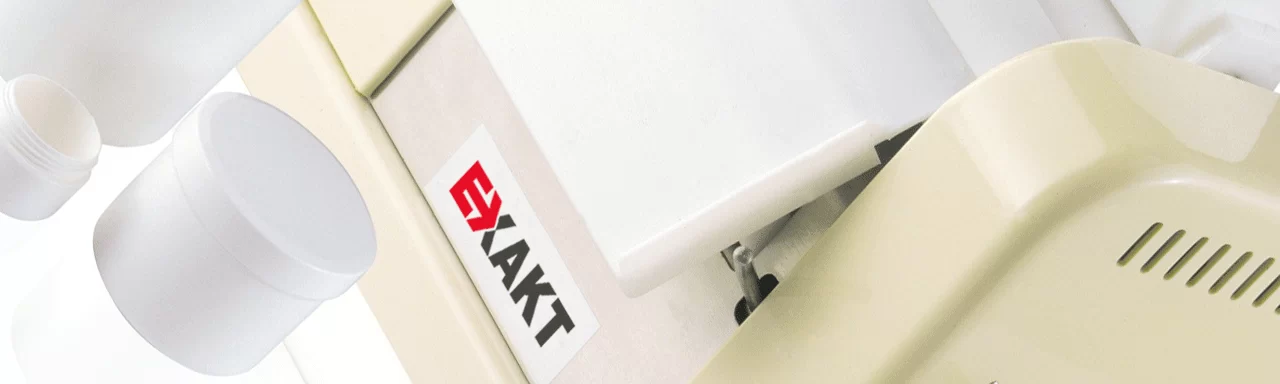
Keep your mill performing at a high level. Often times what you think is a problem with the mill is really just a worn-out scraper and/or guides. If used on a regular basis, EXAKT recommends replacing the scraper and guides every 6 months. For quick ordering, go to the EXAKT parts store.
EXAKT’s Pathology Saw Reduces Bone Dust
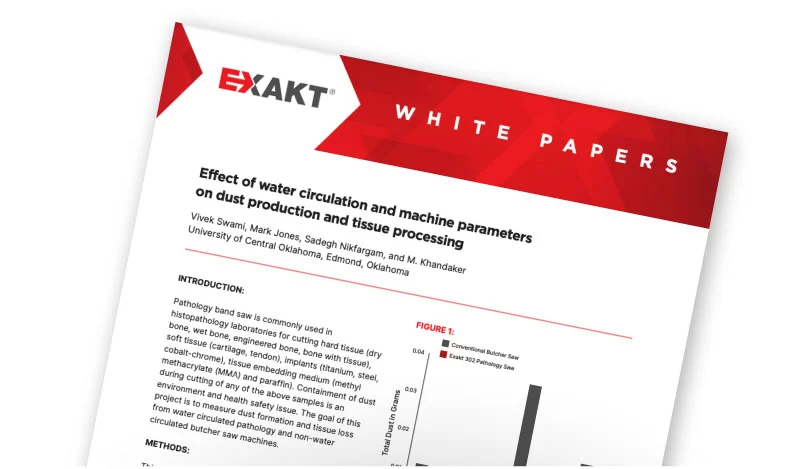
Water flows continuously over the blade, significantly reducing airborne dust and debris Dust and debris during the cutting of hard and soft tissue is an environmental and health safety issue. The goal of this project is to measure dust formation and tissue loss from water circulated pathology and non-water circulated butcher saw machines. Click here […]