The Ointment Mill Process
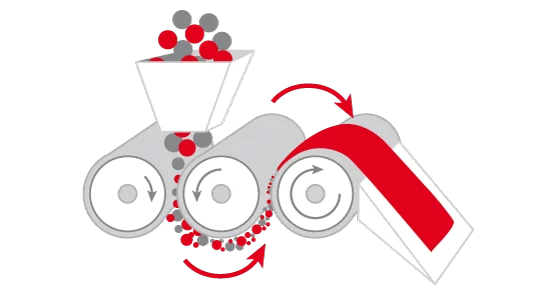
An ointment mill utilizes high shear force to reduce particle sizes, disperse agglomerates, and homogenize viscous materials. Shear force is created by three horizontally positioned rollers rotating in opposite directions and at different speeds relative to each other. The whole product is pulled through the gap between the rollers, resulting in a precise, controllable, and […]