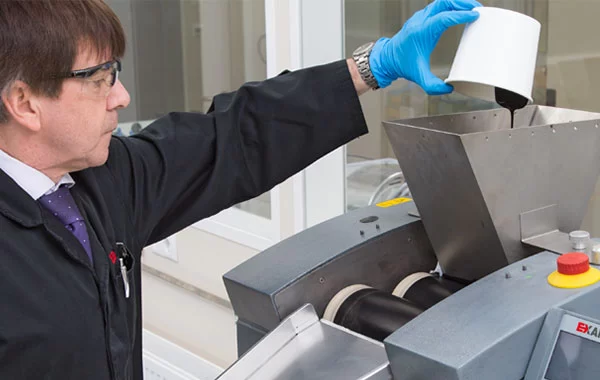
How EXAKT Three Roll Mills Create Better Ceramic Products
EXAKT three-roll mills contribute to the creation of better ceramic products through several key mechanisms: Uniform Dispersion: By effectively breaking down agglomerates and distributing ceramic powders and additives uniformly throughout the matrix, EXAKT three-roll mills ensure homogeneity in ceramic formulations. This leads to consistent material properties, such as mechanical strength, thermal stability, and chemical resistance, resulting in better overall product quality. Controlled Particle Size Reduction: Three-roll mills provide precise control over particle size reduction, allowing manufacturers to achieve the desired