EXAKT Ointment Mills Get Results
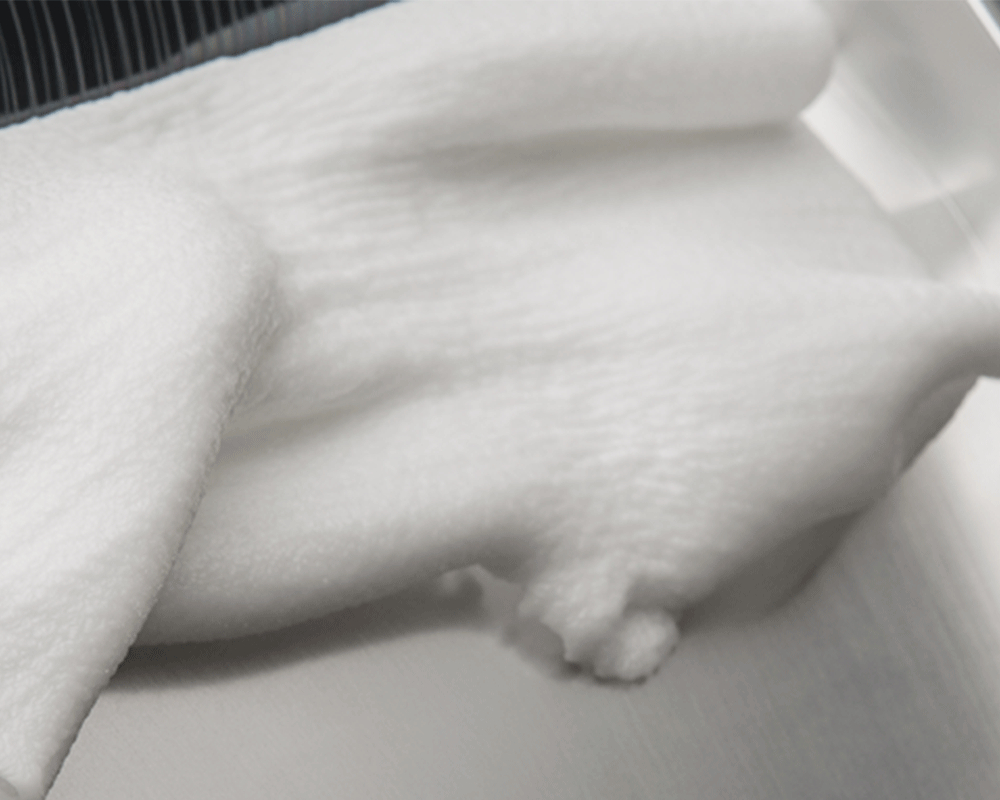
EXAKT three ointment mills deliver results that are consistent and reproducible. A comparative study conducted at the University of Hamburg, Institute of Pharmacy in Hamburg, Germany concluded that the quality of ointments processed with EXAKT ointment mills is better than those processed with electric mixing systems. The study highlighted the following conclusions: The particle size […]
Make Your Mill Safer With the Nip Guard
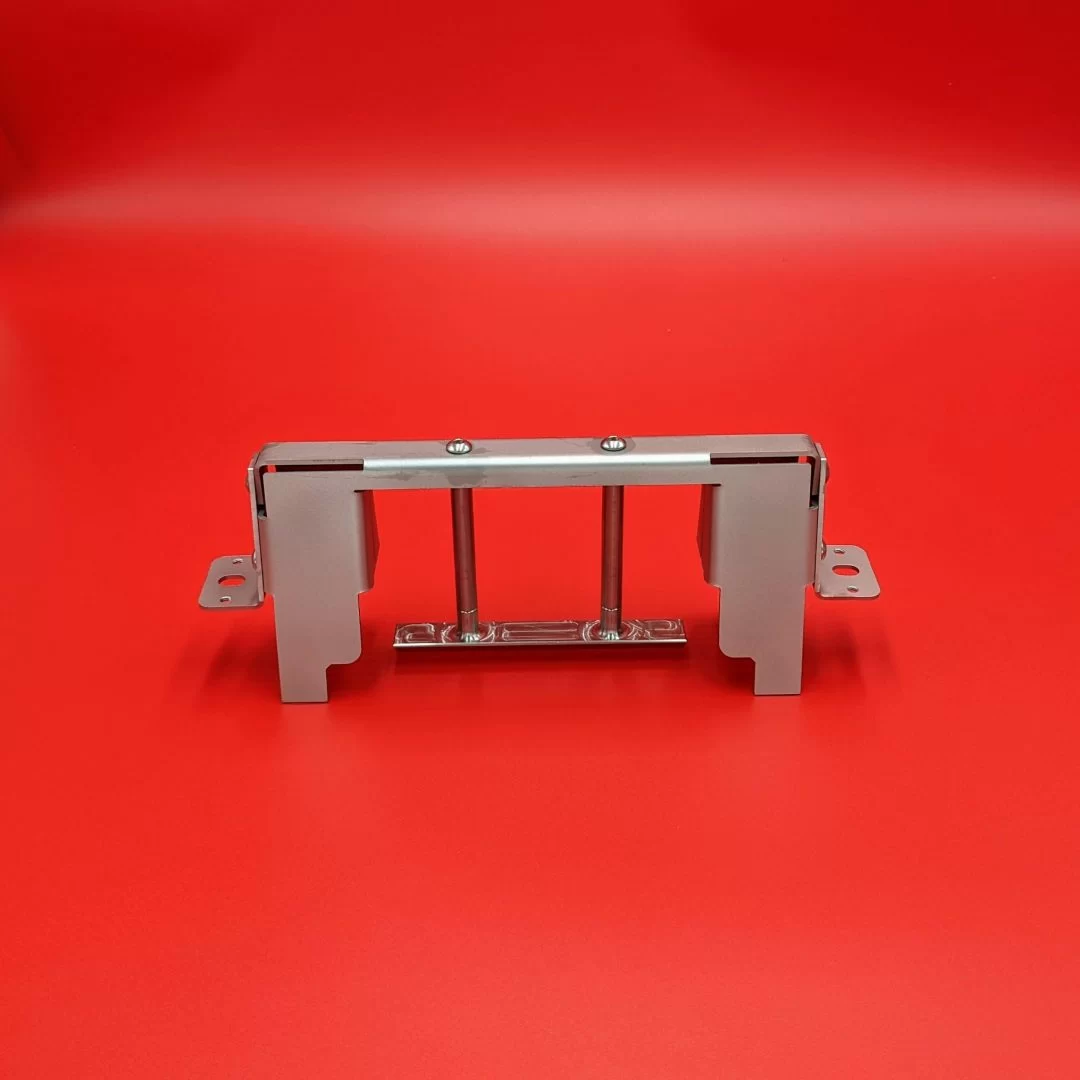
Add an extra layer of safety to your EXAKT 50 I three roll mill. Order here. Make a great mill even better Add another layer of safety Attaches fast – no tools needed Save $$ on costly repairs Keep more of your spatulas Designed for EXAKT 50I use only.
3 Distinct Advantages Using EXAKT Ointment Mills
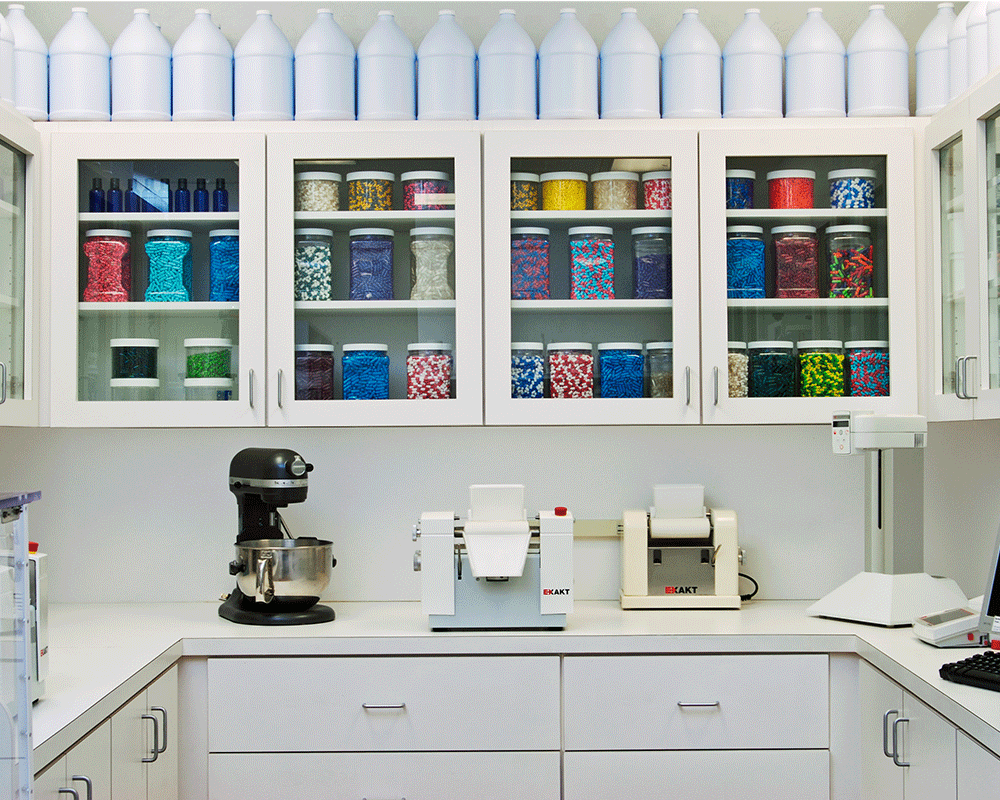
Ointment mills (three roll mills) offer a distinct advantage over other mixing techniques. Only the ointment mill used in the dispersing process guarantees that 100% of the product will be passed through both shear zones. This is why no mixer can do what an ointment mill does. The shear rate between the rollers is the decisive […]
6 Great Features of the 80S Plus
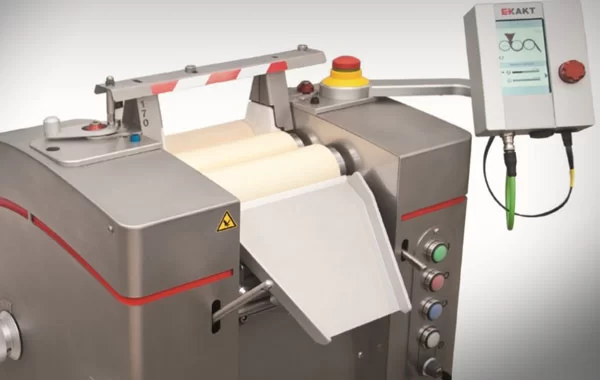
The new EXAKT 80S PLUS has higher safety standards, easier operation, and an even more precise adjustment of the gap. With a powerful motor, optional temperature control, and the choice of ceramic and metallic rollers, the new 80S Plus was designed for processing a wide range of different materials. This three roll mill works well […]
5 Reasons to Choose EXAKT Ointment Mills
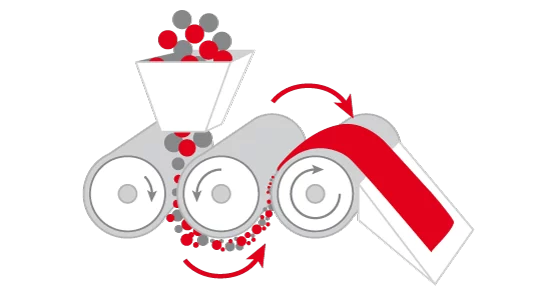
Because precision matters. EXAKT produces the most precise, safe, and user-friendly machines in their respective industries. These products are an investment meant to last. The “Made in Germany” stamp you see on each of our machines embodies the meticulous attention to detail and pride in workmanship. Our equipment is something special, and we want you […]
7 Reasons to Choose the EXAKT 80E Plus Three Roll Mill
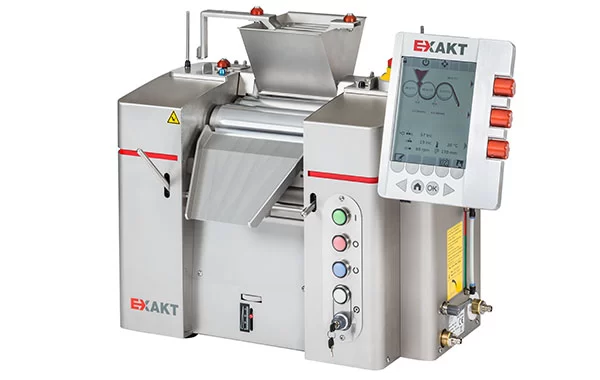
The 80E PLUS three roll mill delivers faster-dispersing results with real-time process analysis. By combining high-precision mechanical design with a state-of-the-art electronic control system, EXAKT has created the new standard for three roll mill technology. Users will have more information than ever before, and the ability to make adjustments on the go. Safe operation mode […]
4 Advantages Using Three Roll Mills
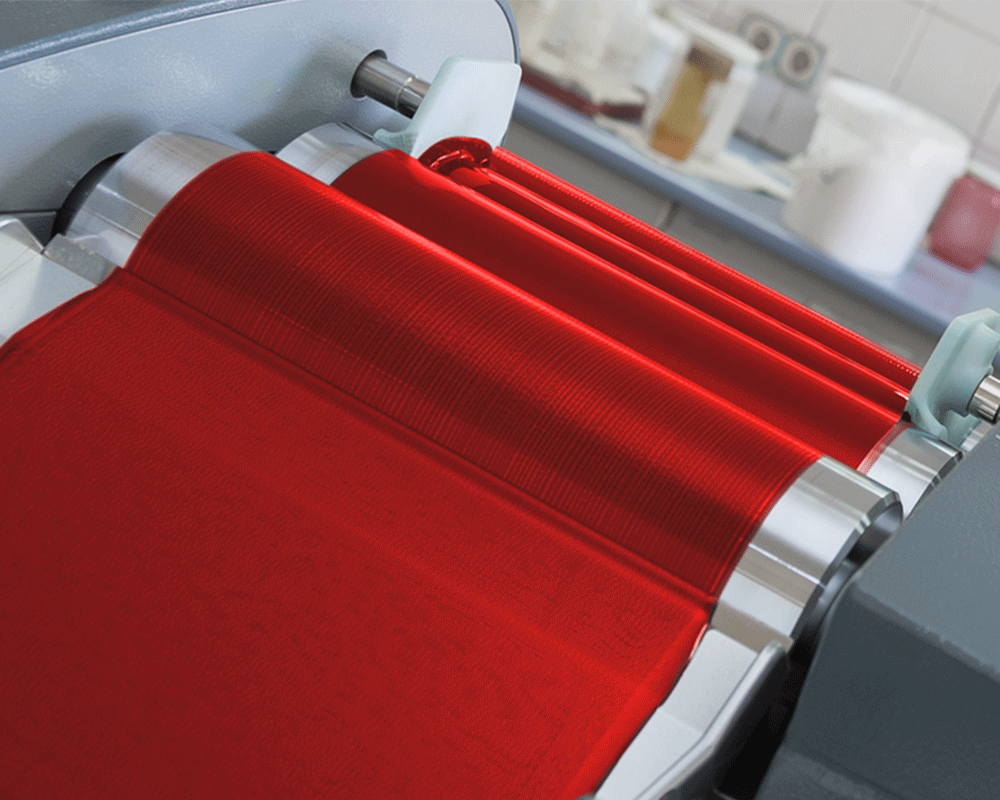
Only the three roll mill used in the dispersing process guarantees that 100% of the product will be passed through both shear zones. The shear rate between the rollers is the decisive factor for the process. This is determined by the roller spacing and the circumferential speed. Agglomerates and powder clumps are broken up and homogenized. […]
Why Choose EXAKT Ointment Mills
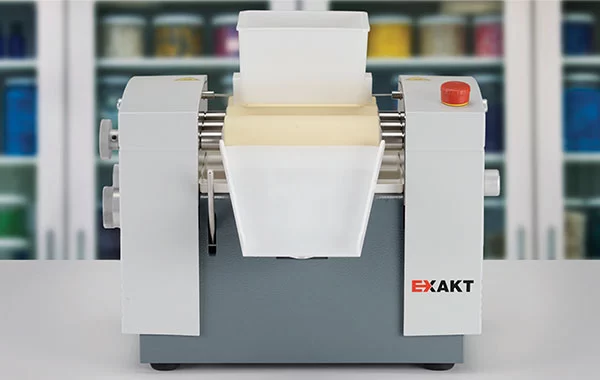
Because precision matters. Experience – More than 60 years in milling compounds, more than 45,000 systems installed worldwide. Expertise – Extensive knowledge of applications with a wide variety of materials. Service – Factory-trained technicians are available to help repair and extend the life of your equipment. Products – Machines are made for the customer with […]
The EXAKT 80E Plus Three Roll Mill
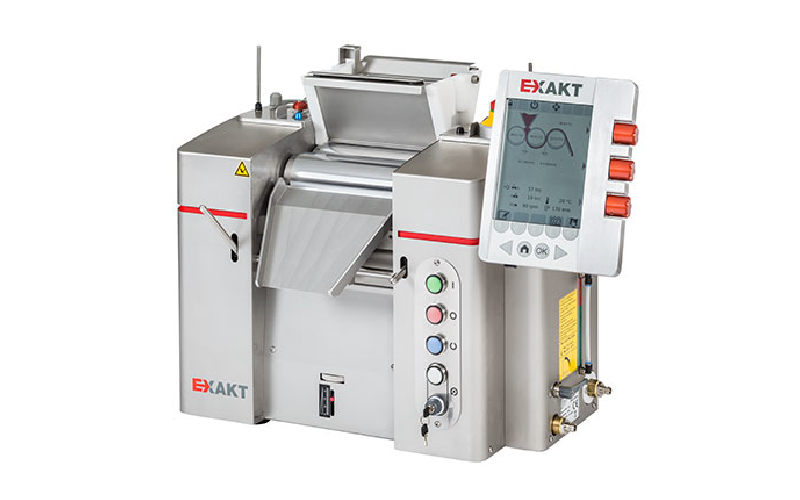
The 80E PLUS three roll mill delivers faster-dispersing results with real-time process analysis. By combining high-precision mechanical design with a state-of-the-art electronic control system, EXAKT has created the new standard for three roll mill technology. Users will have more information than ever before, and the ability to make adjustments on the go. Safe operation mode […]
The EXAKT 80S Plus
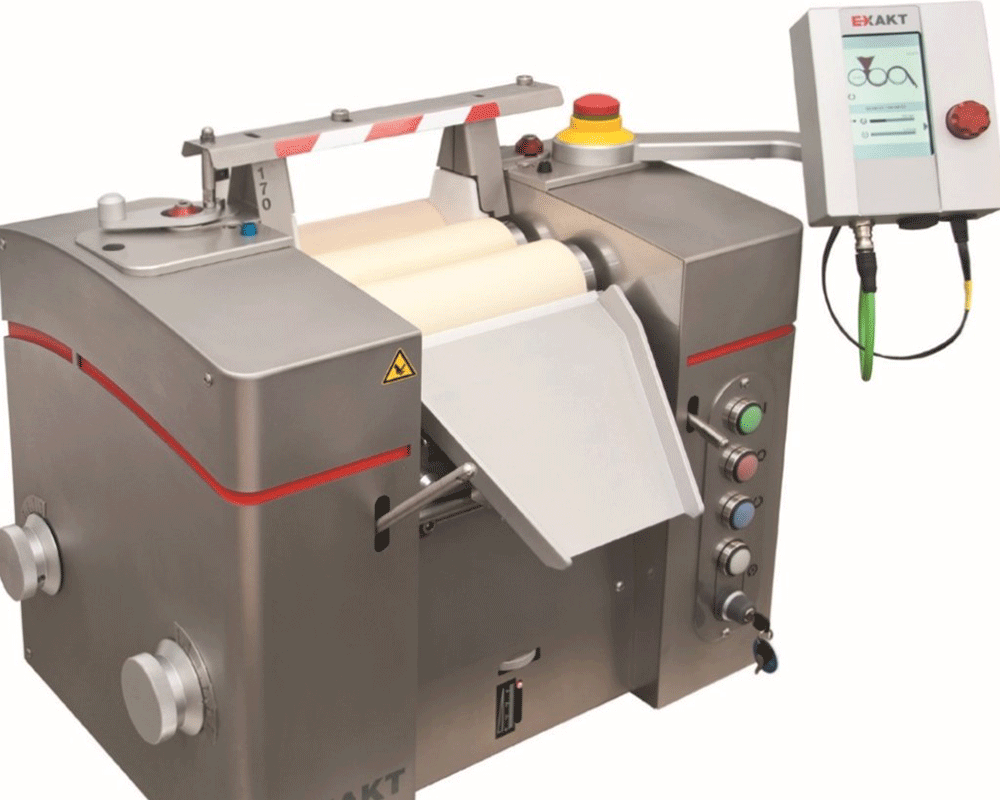
The new EXAKT 80S PLUS has higher safety standards, easier operation, and an even more precise adjustment of the gap. With a powerful motor, optional temperature control and the choice of ceramic and metallic rollers, the new 80S Plus was designed for processing a wide range of different materials. This three roll mill works well […]