3 Distinct Advantages Using EXAKT Ointment Mills
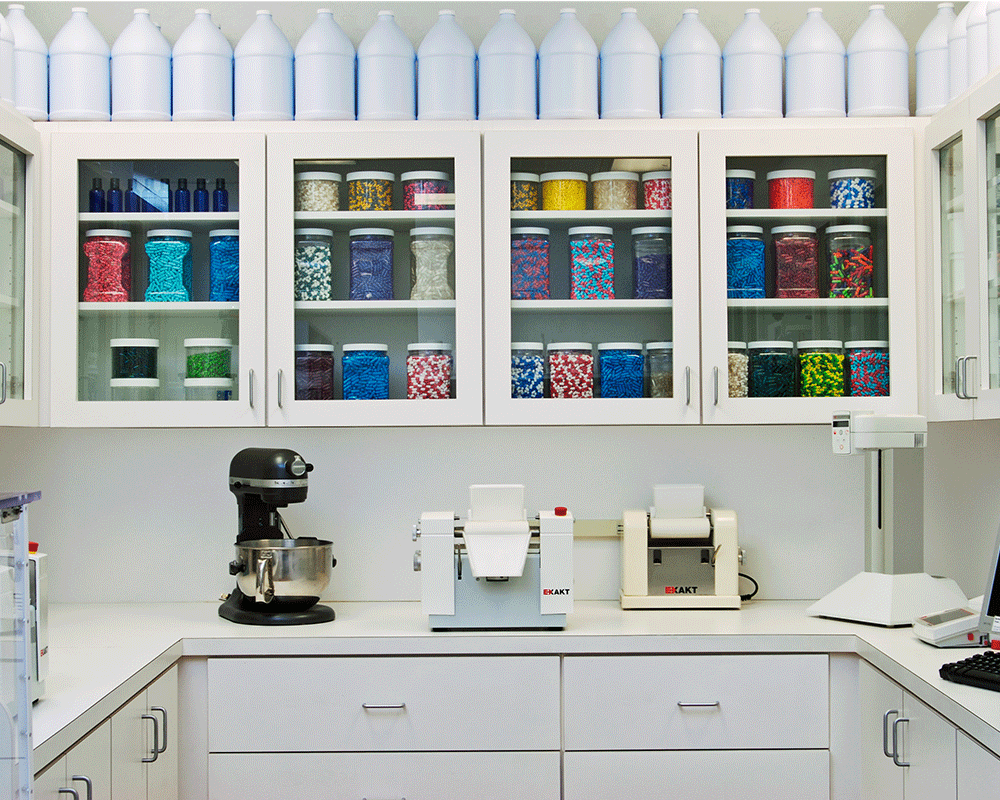
Ointment mills (three roll mills) offer a distinct advantage over other mixing techniques. Only the ointment mill used in the dispersing process guarantees that 100% of the product will be passed through both shear zones. This is why no mixer can do what an ointment mill does. The shear rate between the rollers is the decisive […]
4 Advantages Using Three Roll Mills
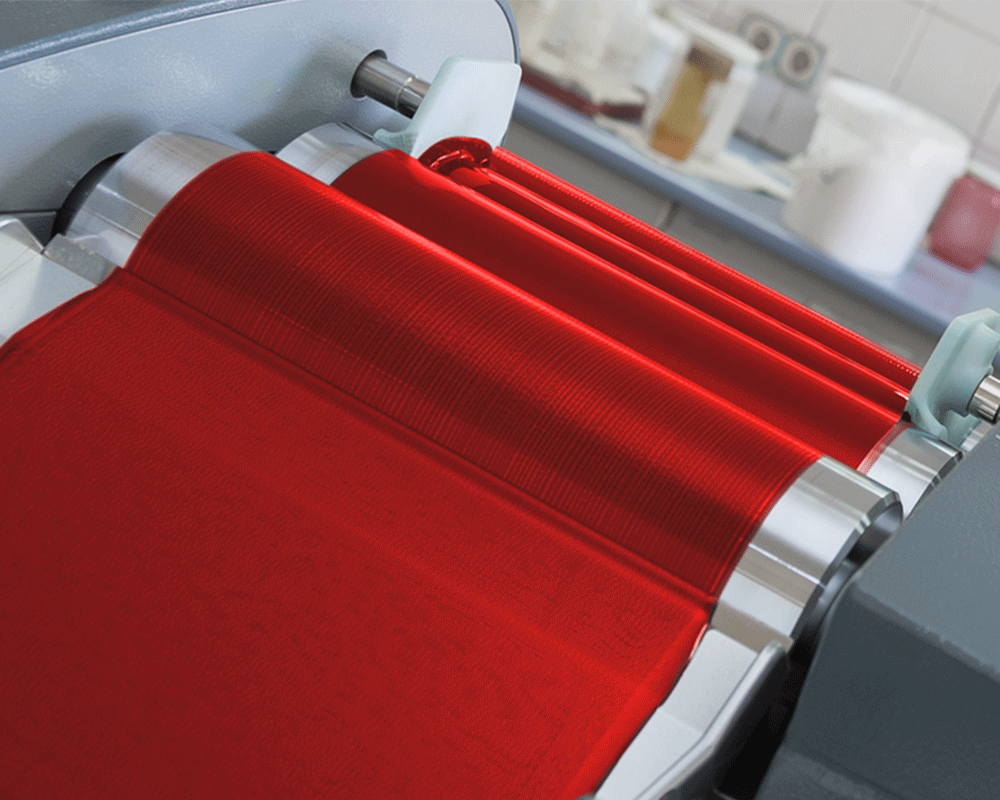
Only the three roll mill used in the dispersing process guarantees that 100% of the product will be passed through both shear zones. The shear rate between the rollers is the decisive factor for the process. This is determined by the roller spacing and the circumferential speed. Agglomerates and powder clumps are broken up and homogenized. […]
Ointment Mill Advantages
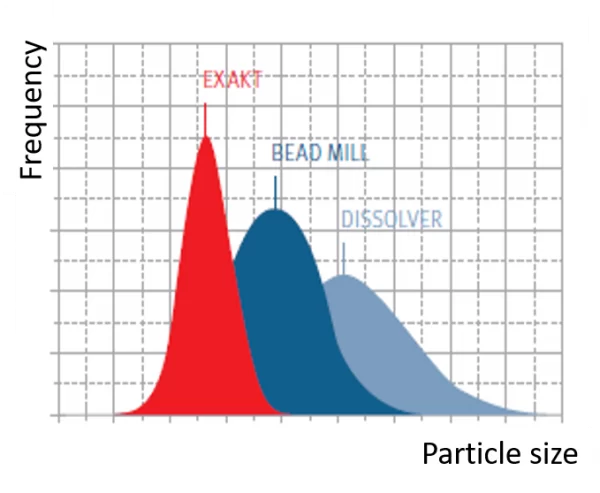
Only the ointment mill used in the dispersing process guarantees that 100% of the product will be passed through both shear zones. The shear rate between the rollers is the decisive factor for the process. This is determined by the roller spacing and the circumferential speed. Agglomerates and powder clumps are broken up and homogenized. […]
Three Roll Mill Advantages
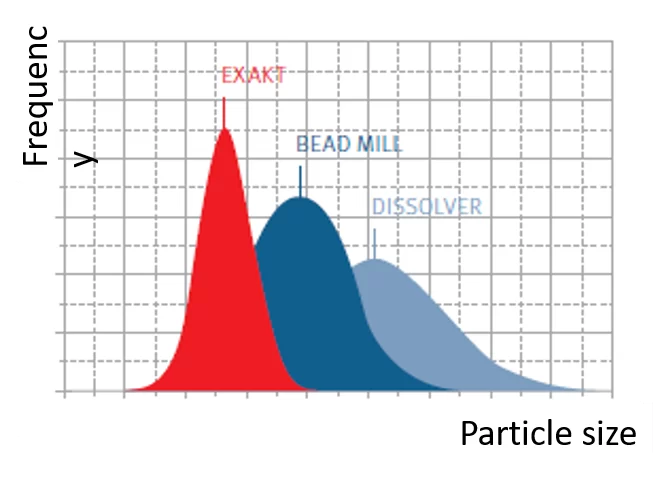
Only the three roll mill used in the dispersing process guarantees that 100% of the product will be passed through both shear zones. The shear rate between the rollers is the decisive factor for the process. This is determined by the roller spacing and the circumferential speed. Agglomerates and powder clumps are broken up and homogenized. […]
What does a three roll mill do?
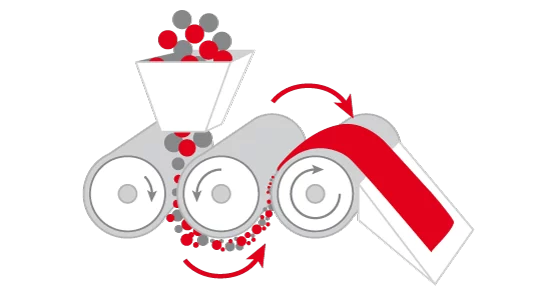
A three roll mill utilizes high shear force to disperse agglomerates, and homogenize viscous materials. Shear force is created by three horizontally positioned rollers rotating in opposite directions and at different speeds relative to each other. The product is pulled through the gaps between the rollers. Agglomerates and powder clumps are broken up and homogenized. […]
Three Roll Mills for Cosmetics

Cosmetic Manufactures Use EXAKT Three Roll Mills For Brilliant Colors When it comes to color brilliance, color effects and high color intensity, EXAKT Three Roll Mills offer significant advantages. For example, the primary particles are not damaged during the processing of metallic and effect pigments. Optimal process control and reproducible quality are a matter of […]
Improve the Performance of Your Ointment Mill.
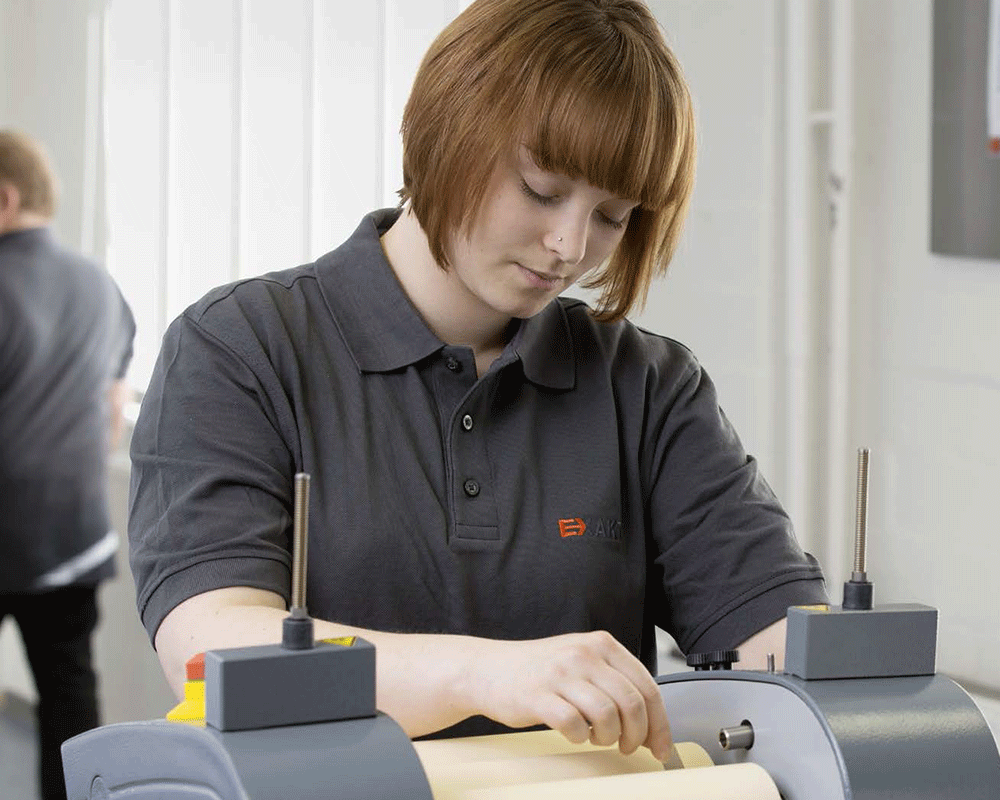
Your Ointment Mill May Need a Tune-up EXAKT ointment mills rarely require repair, but sometimes a tune-up can help improve the performance of your machine and provide years of worry-free use. For smaller mills, we can turn your mill around the same day it’s received at our shop to minimize downtime. For larger mills, simply […]