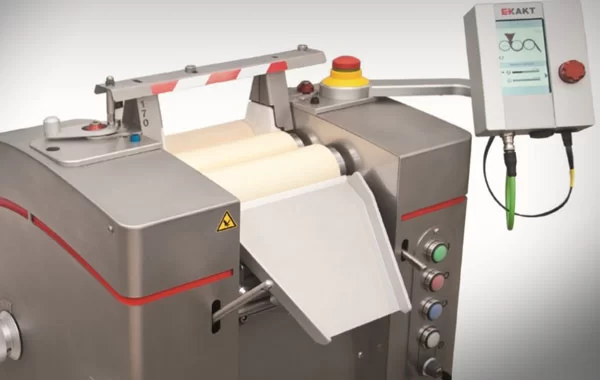
6 Highlights of the EXAKT 80S Plus
Improved safety standards, easy operation, and even more precise adjustment of the gap. The EXAKT 80S PLUS has higher safety standards, easier operation, and an even more precise adjustment of the gap. With a powerful motor, optional temperature control, and the choice of ceramic and metallic rollers, the 80S Plus was designed for processing a wide range of different materials. This three roll mill works well with both small quantities in the laboratory and larger production quantities. Different working widths