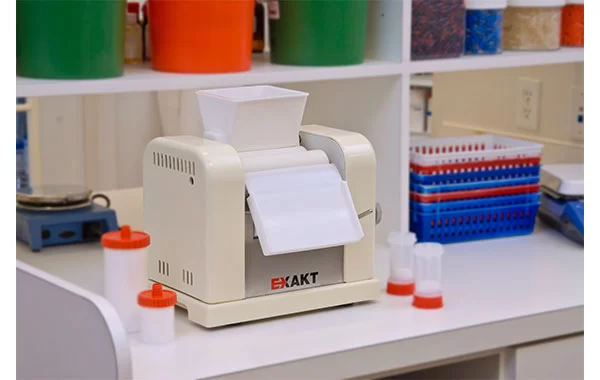
5 Special Highlights: EXAKT’s Classic 50 Ointment Mill
With more than 30,000 units installed around the world, the EXAKT Classic 50 is the best-known and most accepted pharmaceutical ointment mill. The Classic 50 ensures excellent results for topical, oral, and suppository applications. When preparing ointments and creams containing crystallized ingredients, the EXAKT 50 is superior to even highly advanced mixing technologies. Applications: suspension ointments, emulsions ointments, or cream. Highlights: Particle fineness to below 20 microns Up to 7 liters/ hour throughput Chemically inert porcelain rollers Mechanical overload protection