Why Choose EXAKT Ointment Mills
Because precision matters. Experience – More than 60 years in milling compounds, more than 45,000 systems installed worldwide. Expertise – Extensive knowledge of applications with a wide variety of materials. Service – Factory-trained technicians are available to help repair and extend the life of your equipment. Products – Machines are made for the customer with […]
Why Choose EXAKT Three Roll Mills?

Because precision matters. Experience – More than 60 years in dispersion, more than 45,000 systems installed worldwide. Expertise – Extensive knowledge of applications with a wide variety of materials. Service – Factory-trained technicians are available to help repair and extend the life of your equipment. Products – Machines are made for the customer with the […]
EXAKT Three Roll Mills for Grease and Lubrication
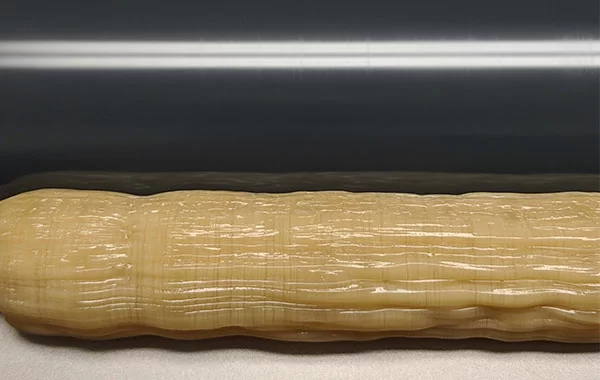
Chemical engineers use EXAKT three roll mills to improve penetration values and reduce noise in grease and lubrication formulations. Precise, compact, and efficient, these mills are among the most user-friendly devices in the industry. Learn more at EXAKTDispersion.com
Cosmetic Applications – EXAKT Three Roll Mills
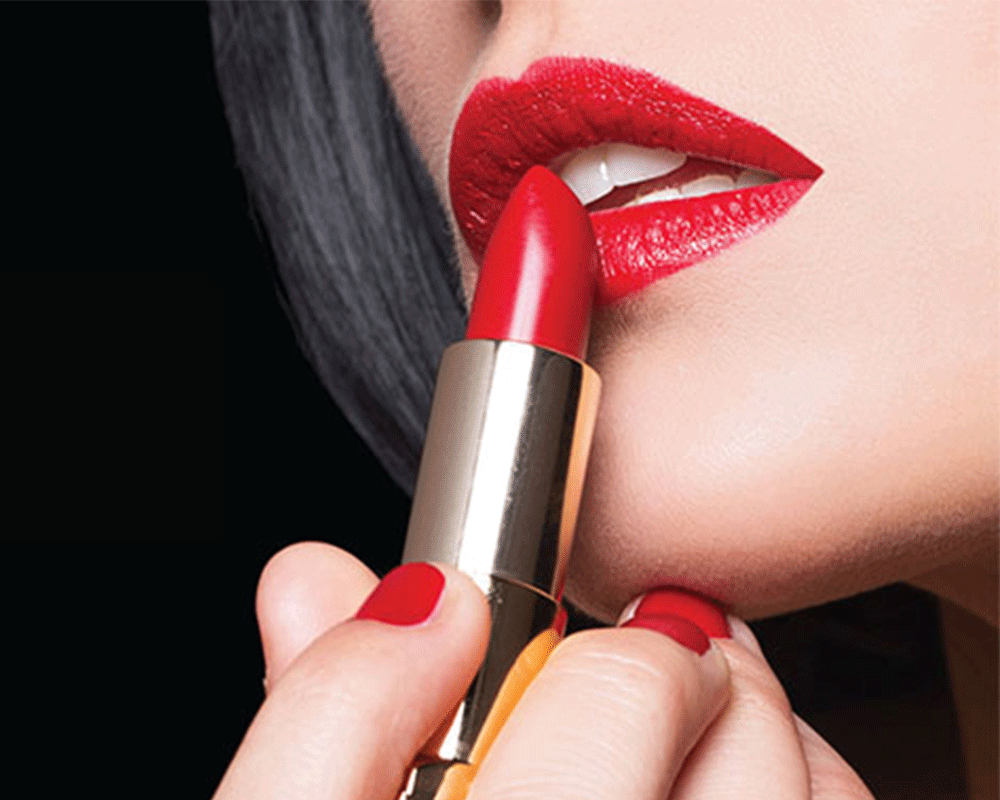
EXAKT Three Roll Mills ensures consistent and vibrant color in cosmetics by evenly dispersing pigments into creams, gels, and other formulations. The precision gap control of the rollers enables ultra-fine grinding, eliminating clumps and streaks for a smooth, uniform finish. This enhances the color intensity and stability of lipsticks, foundations, and eyeshadows. By reducing particle […]
Check Out The New 80S Plus!
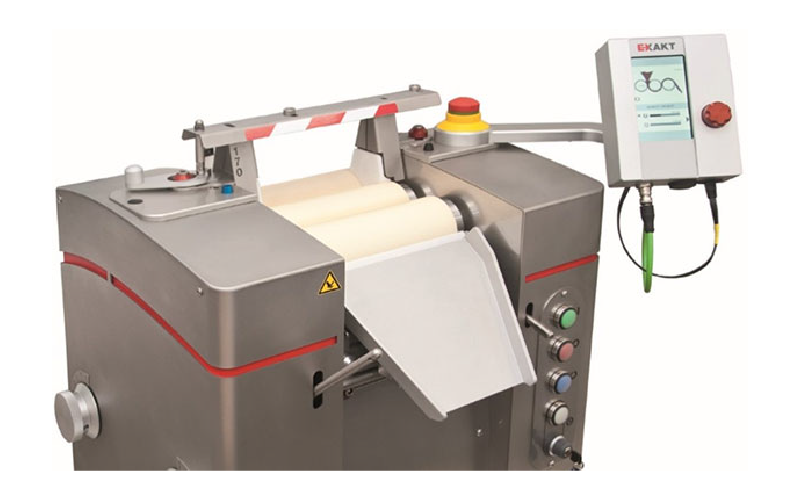
For maximum fineness, higher throughput. The S-Line series is the entry point for achieving the finest dispersing results. Highlights: Easily monitor speed, temperature, production timer, and power consumption. Adjustable gap range: 5 to 230 µm Variable throughput from as little as 10 ml up to 18 l/h at a 10 μm gap Covers made of blasted […]
Have you seen the new EXAKT 80E Plus?
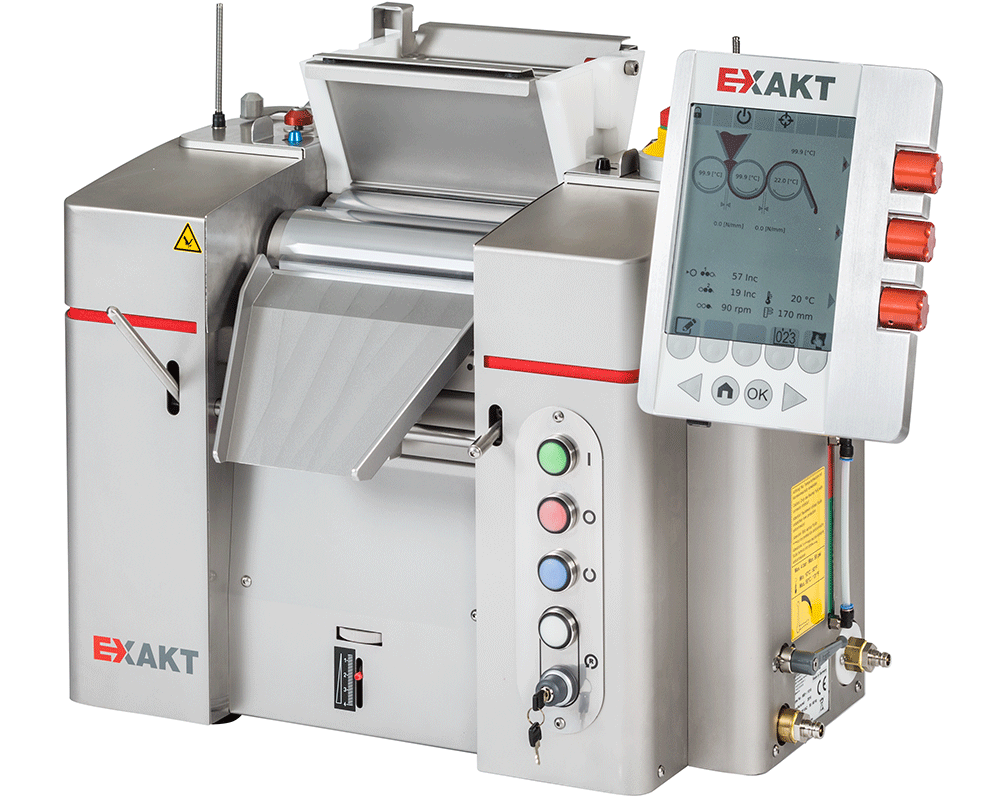
Smarter, Safer, Faster Experience our most advanced three roll mill Smarter See real-time analysis of the dispersion process Identify problems before they get out of control Make quick and easy in-process corrections on the go Monitor temperature changes during the process Facilitate quicker process optimization Provides easy download of process conditions for quality control and purposes Safer The safest […]
Your Three Roll Mill May Need a Tune-up
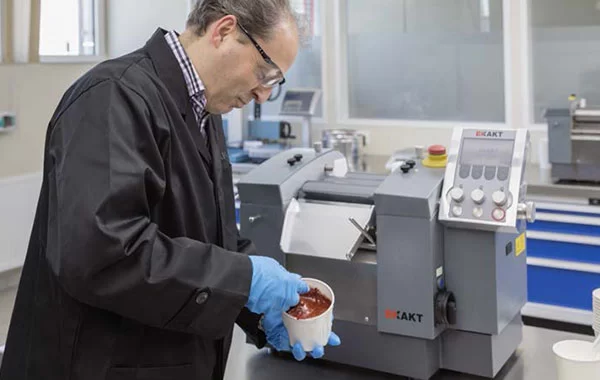
Has your three roll mill been serviced in the last two years? EXAKT three roll mills rarely require repair, but sometimes a tune-up can help improve the performance of your machine and provide years of worry-free use. For smaller mills, we can turn your mill around the same day it’s received to minimize down […]