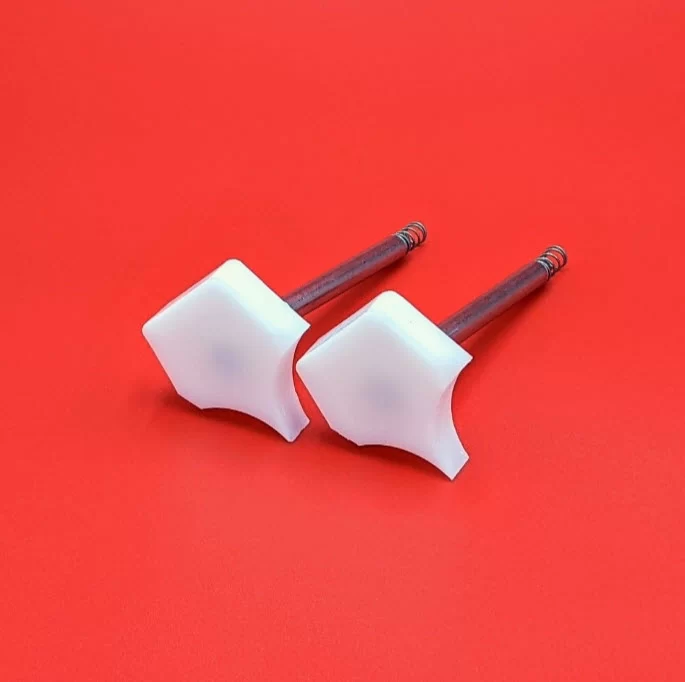
Time to replace your guides and scraper?
Keep your mill performing as it should. Often what you think is a problem with the mill is just a worn-out scraper and/or guides. If used regularly, EXAKT recommends replacing the scraper and guides every 6 months. For quick ordering: https://exaktusa.com/shop/. Or email: exaktorders@exaktusa.com.